Solution Finder
FIND THE RIGHT SOLUTION FOR YOU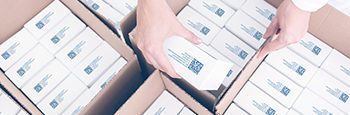
Aggregation Solution
Aggregation takes you beyond unit-level traceability to see the whole picture
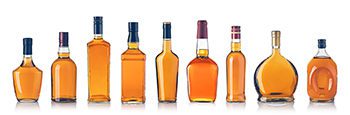
Anti-counterfeiting
Stop counterfeiting, protect your brand and gain greater consumer confidence
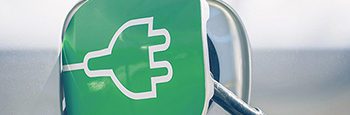
Battery Traceability
Contribute to a better environment through battery traceability
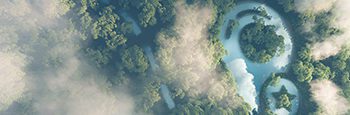
Carbon Tracking
Measure and track your environmental footprint across your supply chain
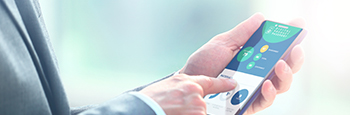
Digital Product Passport (DPP)
Find out about OPTEL’s approach to overcoming the challenges associated with the European Union’s upcoming Digital Product Passport. Learn how we do it differently.
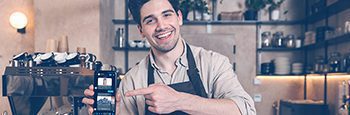
Engagement Programs
Engage directly with consumers to optimize your marketing programs
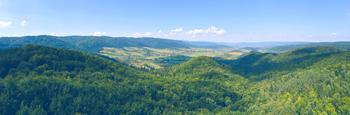
EUDR Compliance Simplified
Optchain’s EUDR software links commodities to their production plots using data capture tools tailored to your supply chain, operations and processes.
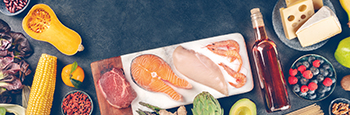
Food Safety Compliance
Improving food safety and integrity through supply chain traceability
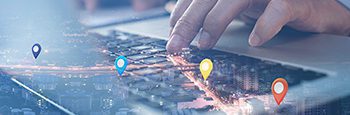
Inventory Tracking and Planning Solution
Manage your inventory like never before: real-time visibility on asset inventory levels, geolocation and expired date tracking
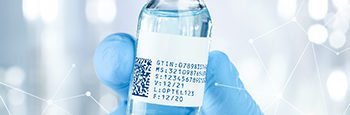
Line Automation
Production Line Automation Solutions: from the case packer to the end-of-line Cobot Palletizer, discover OPTEL’s high performing and turnkey automated line solutions.
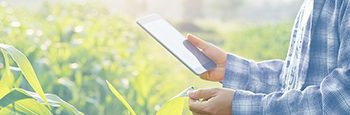
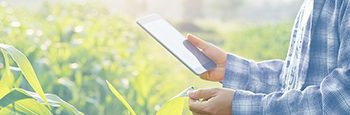
Operational Efficiency
Optimize your production efficiency with strong analytics and reliable, real-time data for the agribusiness
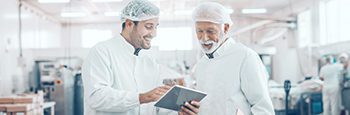
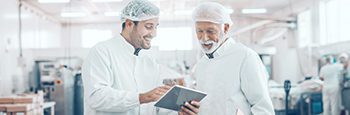
Operational Performance
Optimize your production efficiency with strong analytics and reliable, real-time data for the CPG, food and beverage industries


Optchain for ESG Compliance and Traceability
Optchain is a supply chain platform focused on ESG compliance, automating data collection, improving visibility, and delivering insights.
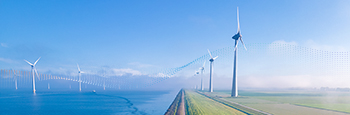
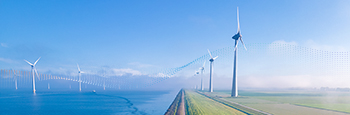
OPTCHAIN for CBAM Compliance
Optchain offers an all-in-one solution for CBAM compliance. Track scope 1, 2, and 3 emissions and submit XML reports.
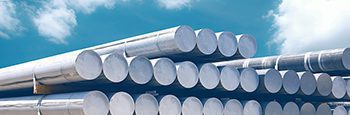
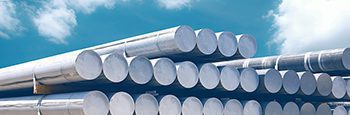
Product Authentication for Metals and Minerals
Authenticate any product, any time, anywhere for total consumer confidence and regulatory compliance
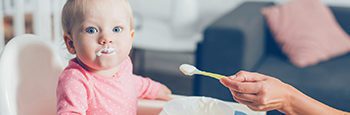
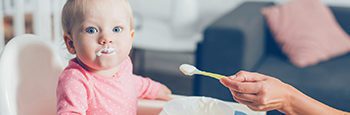
Product Quality
Traceability for visibility, precise and more efficient recalls, and raw-material traceability
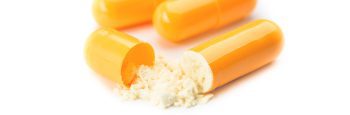
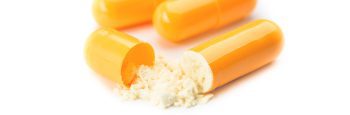
QR Code Verification
Drugs Rule 2022 in India: Discover OPTEL’s QR Code Verification Solution
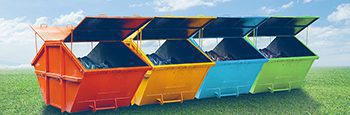
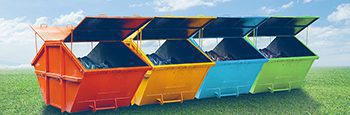
Traceability for the Residual Material Industry
Know the where, when and how of all your material disposal
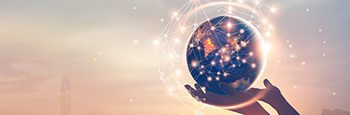
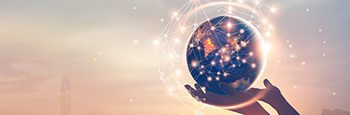
Responsible Sourcing
Trace materials back to the source to ensure and prove sustainability
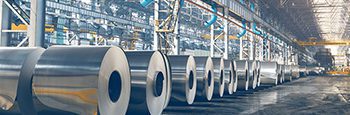
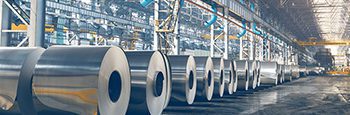
Responsible Supply Chain – Metals and Minerals
Ensure metals and minerals are responsibly sourced and environmentally sound
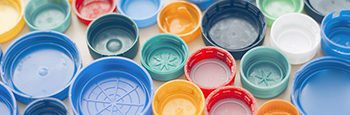
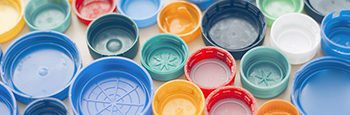
Reusable Packaging Management
Trace and monitor your reusable assets from manufacturing to end user and back
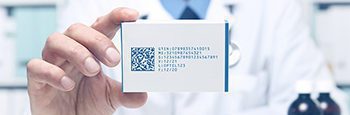
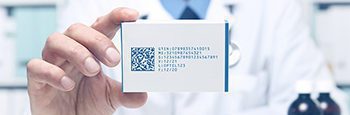
Serialization Solution
Serialization is the first step in the traceability journey. OPTEL delivers scalable pharma solutions for global compliance and end-to-end visibility.


Site Level Solutions (L3)
Manage your plant-level serialization operations with the latest technology
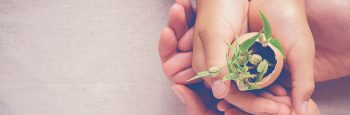
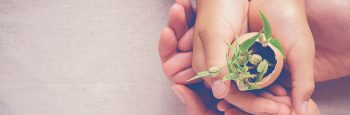
Sustainable Supply Chain
Ensure ingredients and raw materials are responsibly sourced and environmentally sound
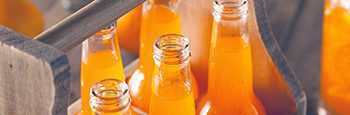
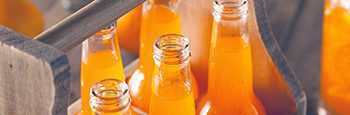
Tax Management Solutions
OPTEL offers a scalable and modular Tax Management Solution that uniquely marks, inspects, tracks, traces and validates your products throughout the supply chain. Comply with regulations, mitigate counterfeit, and gain access to valuable data.
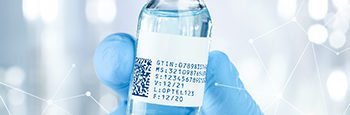
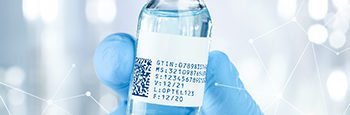
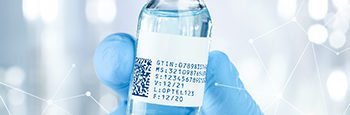
Track-and-Trace Solutions for the Pharmaceutical Industry
Gain supply chain visibility and assured traceability with audits and certifications
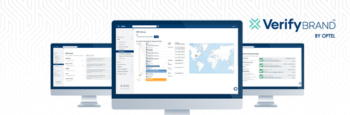
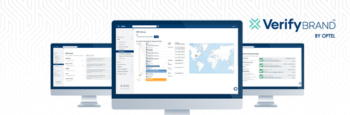
VerifyBrand™ Supply Chain Integrity Solution
Discover OPTEL’s VerifyBrand™ Real-Time Serialization and Traceability software for Compliance, Product Authentication, Brand Protection and Inventory Optimization.
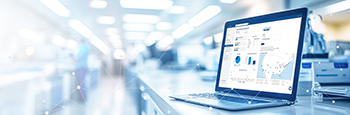
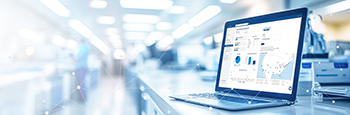
VerifyBrand™ for the Pharmaceutical Industry
VerifyBrand™ is an essential tool to comply with most of the world’s pharmaceutical regulations
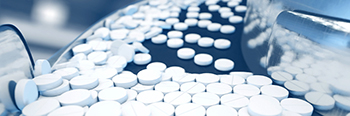
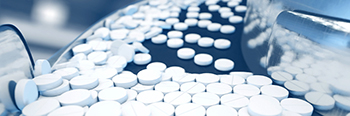
Vision Systems
Discover OPTEL’s unmatched Vision Systems with AI capabilities. Our Visions Systems can inspect any product with high accuracy to ensure product safety and quality.
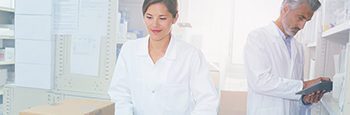
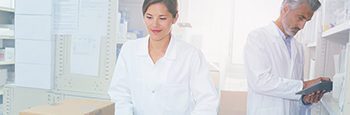
Warehouse Management Solution
Manage your distribution and warehouse serialization process